CNC machining, also known as Computer Numerical Control machining, has become a cornerstone of modern manufacturing. It offers an unmatched level of precision, reliability, and consistency previously impossible with traditional techniques. Automating the operation of machines using computers CNC machines allow companies to create complex components with remarkable accuracy. From aerospace and automotive industries to electronic and healthcare, CNC machining is utilized throughout the world to make complex components that need high precision. Computers’ integration into the manufacturing process has revolutionized how products are created and made, establishing new standards for quality and productivity.
The core feature of CNC machining lies the ability to convert digital models into physical parts. By using computer-aided design (CAD) software, engineers and designers create intricate 3D models of their desired part. This digital design is then transferred into precise instructions known as “G-code,” which the CNC machine uses to execute actions like cutting, drilling, or milling. Digital control provides an extremely high degree of precision that manual milling cannot achieve. This also means that once a design is programed in the machine it can be repeated in perfect synchronization, resulting in identical components in huge quantities with no manual adjustments. This repeatability is essential in industries where precision and homogeneity are vital.
Alongside its accuracy, CNC machining is also acknowledged for its speed and value. Conventional machining processes typically require experienced operators to regulate and adjust the machinery and can take a long time and expensive. CNC machines eliminate a large portion of the manual work required in production and can operate in complete autonomy for extended time after having been put in place. This permits manufacturers to expand their productivity without needing the need to increase their labor or other resources. In addition, CNC machines are capable of performing multiple operations within a single set-up which reduces the requirement to transfer parts and reposition them this saves time and lowers the likelihood of error. The automation results in quicker manufacturing cycles as well as lower cost per component, making CNC machining an attractive solution for firms who want to simplify the manufacturing process.
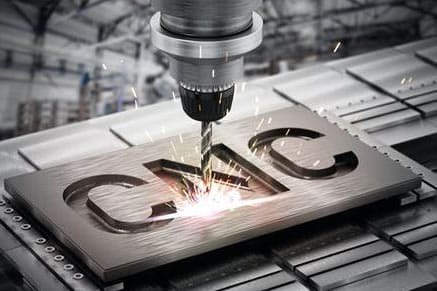
CNC machine’s flexibility is another reason it has become an integral part of the modern production. The technique can be utilized with a wide range of substances, ranging from metals such as titanium and stainless steel to plastics and wood. This makes CNC machining suitable to make parts suitable for diverse industries including automotive, aerospace, electronic and medical consumer products. In addition, CNC machines can perform many different operations including cutting, milling, drilling, engraving, and even 3D contouring with a single configuration. The multi-functionality of CNC machines eliminates the need to have multiple machines as well as part transfers, which further improves efficiency. When it comes to making prototypes or manufacturing large volumes of products, CNC machining offers the flexibility to meet diverse needs in production. To obtain new details please go to Premiumparts
One of the difficulties associated with CNC machine machining is the cost of initial setup. Investing in CNC machinery as well as the software to manage the machine can be costly particularly for small-sized businesses. However, the long-term benefits of CNC machining–such as reduced labour costs, improved efficiency and better production quality often outweigh any initial investment. Furthermore, many businesses offer CNC machining services to businesses that do lack the funds to make the investment in their machines, which allows smaller companies to make use of this technologies without having to pay upfront. As the demand for CNC machineries continues to increase, the cost of machinery and software is predicted to lower, making it available to a greater number of companies.
It is predicted that the future for CNC Machining looks bright the advancements in technology are constantly increasing the capabilities of what machines can do. While CNC machines grow more sophisticated, they are increasing integrated with other technologies that include 3D printing and robotics, to create hybrid manufacturing processes that blend the benefits of a variety of techniques. In addition, the growth of smart manufacturing as well as technology like the Industrial Internet of Things (IIoT) is enabling greater connection and automatization in CNC machining, allowing machines to communicate with each to adjust their processes with real-time sensors’ data. As new technologies continue to progress, CNC machining will remain a vital tool in the development of modern manufacturing and will provide even more precision as well as speed and flexibility in the future of manufacturing.